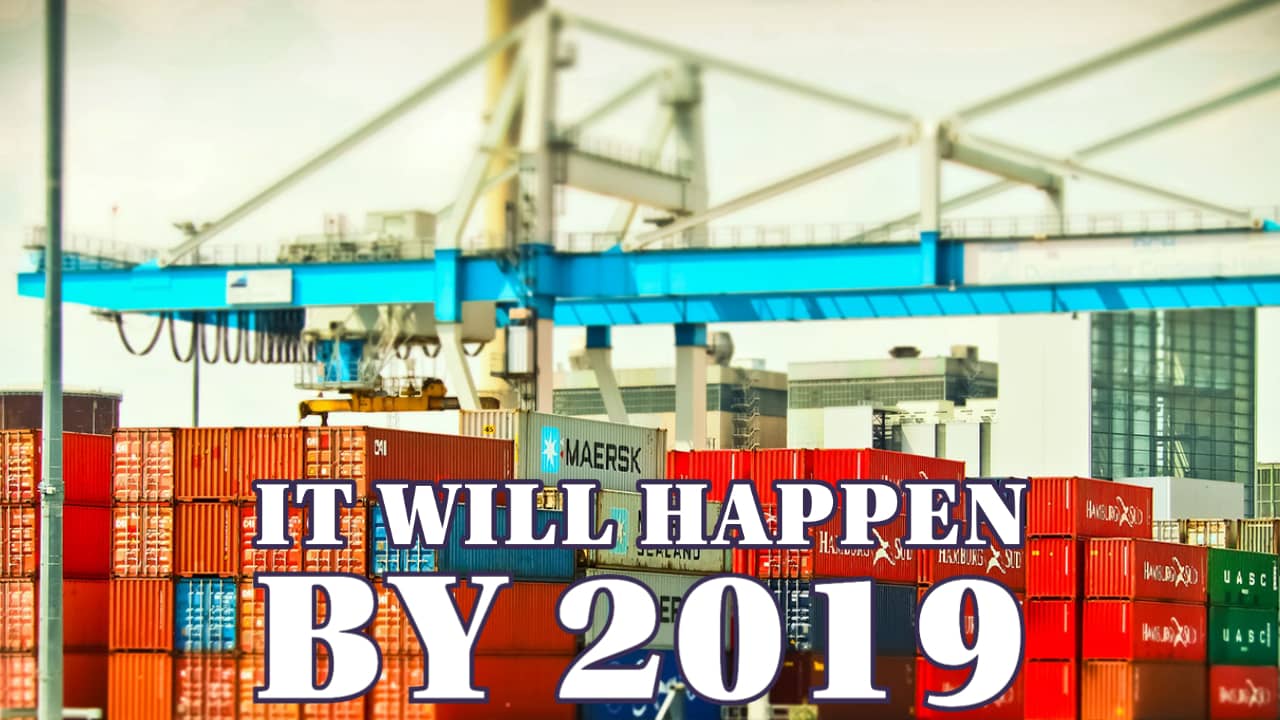
How Ports of Auckland Automation Will Affect Importers
5-minute read
Progress is being made on the massive automation project being undertaken at the Ports of Auckland , as the port readies itself to become the first in New Zealand to use automated straddle carriers to load and unload trucks and to operate the container yard.
There is also a “world first element to the project as while there are automated terminals overseas ~ Patrick’s Botany terminal has been fully automated since 2015, for example ~ this as I understand it is the first time that a hybrid operation has been planned where the current manually-driven straddles are retained and have to interface with automated straddles.
How the project is being achieved is fascinating. I toured the Fergusson terminal recently to see what progress had been made since I was last there late in 2017 and saw how the project team is having to make do with tiny pockets of space to erect and trial the auto strads.
The team has no option – Fergusson is a major working terminal which is already under space pressure. So the Kone team erecting the strads have to make do with a small area not far from where imported vehicles are marshalled, and the testing team have a handkerchief-sized area on the northeast rip of Fergusson where the strads can be calibrated and put through their paces.
This includes several hours of endurance tests, where the straddles must complete repeated tasks without fail.
Close to the test area is a prototype truck grid including a steel backstop for the wheels of the truck or trailer, so the vehicle can be backed-up to exactly where the auto strad is expecting it to be.
The engineering workshops weren’t big enough to accommodate the height of the new straddles, so a special shed has had to be rigged up using stacks of containers as the walls, topped by a curved canopy roof.
Despite these challenges, the project is on target to go live late next year and deliver immediate benefits.
The newly automated straddle carriers will be 15.8 metres tall and will be able to stack containers up to four-high.
Currently, the terminal uses the 13-metre-tall manual straddles, which stack containers up to three high. Therefore this switch will immediately increase stacking capacity by a third. A new reefer area on the south-east corner of Fergusson will also stack four high but will be commissioned before the automation project going live, and until then will be used to three-high.
Also, the automated straddles require fewer “roadways” (clear pathways where the manual straddles move around the blocks of container stacks) which means the yard layout can be tweaked to achieve greater stacking density, again increasing capacity.
Automation will also help to make operations more sustainable by reducing emissions, noise and light pollution, and will keep costs down .
In total 27 auto straddles have been ordered of which 18 have arrived already and 14 of which are erected and mobile. All remain under the ownership of Kone until they have been tested proven fit for purpose and are accepted by PoAL.
A natural question to ask is why, if the auto strads offer so many operational and cost advantages in the yard, they aren’t going to also do the transfers between the yard and ship-to-shore cranes?
The answer is that the port believes productivity would be lost if that part of the operation was automated. Results from operations overseas suggest that the moves per hour attained by automated transfers are well below manual rates.
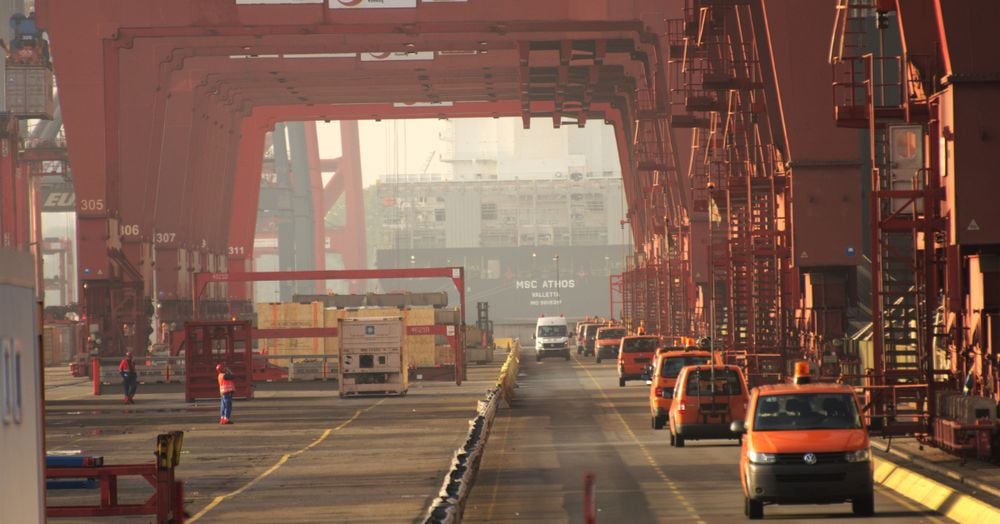
Also, the manual straddles at Fergusson lift two boxes whereas the auto strads will only lift one at a time. So a hybrid operation has been devised where the manual strads can drop two boxes in a buffer area, and the automated strads can pick them up individually and complete the stacking operations and the vehicle transfers.
The actual construction and operation of the straddles themselves is only one part of the project.
Automation and extension of the truck grid require the installation of positioning and control systems, and a new perimeter fence and gates to separate people from the automated equipment. All will have to go through full system testing before being commissioned.
New extra-rigid lighting poles have had to be installed upon which the signal transmitters can be mounted. The old poles were prone to movement in high winds, meaning the signals may not have been as accurate as the guidance system requires. The new poles overcome that issue.
Other works which have needed to dovetail with the automated system include updating the vehicle booking system (VBS) for truck arrivals on the grid and improved optical character recognition (OCR) for the scanning of container numbers.
All of these must also fit in with the Fergusson Container Terminal Extension project that has been underway since the early 2000s.
A reclamation (consented in 1998) will increase the yard area by several hectares. It also includes a 50-metre extension northward of the main
Fergusson Terminal wharf which was completed in 2015 and the creation of a new Fergusson North Wharf:
This new wharf will extend 296 metres east from the north-west tip of the current Fergusson Terminal wharf, across the north face of the reclamation. Construction started in October 2015 and when complete it will give container terminal a much-needed deepwater third berth.
Three new quay cranes ordered from Shanghai Zhenhua Heavy Industry Co. (ZPMC) for the wharf will arrive later this year. These will be able to cany up to four containers at once, so we will be able to load and unload ships faster.
This is also the wharf that would be extended a further 30 metres to the east under the port’s 30-year Master Plan – the plan which aims to cover the next 30 years until a new port is ready, wherever that may be.
There is another aspect to this whole project which needs to be mentioned, and that is the human aspect – the workforce that will be affected by automation.
There is no doubting there will be job losses, and probably not just among stevedores. There will be some who choose redundancy or retirement but there will be others who want to stay or need to have a future career pathway. For that reason, the port company is undergoing a “futures” initiative with its workforce to see how many wish to retrain for new positions within the port or outside, such as becoming truck drivers.
Others will be offered the chance to learn a new trade at a polytechnic, with the support of the port.
Two containers have been set up with an exhibition, tracing the changes which have occurred in the port’s operations and in New Zealand life generally since the 1980s, and then asking the question “what could the future hold?”
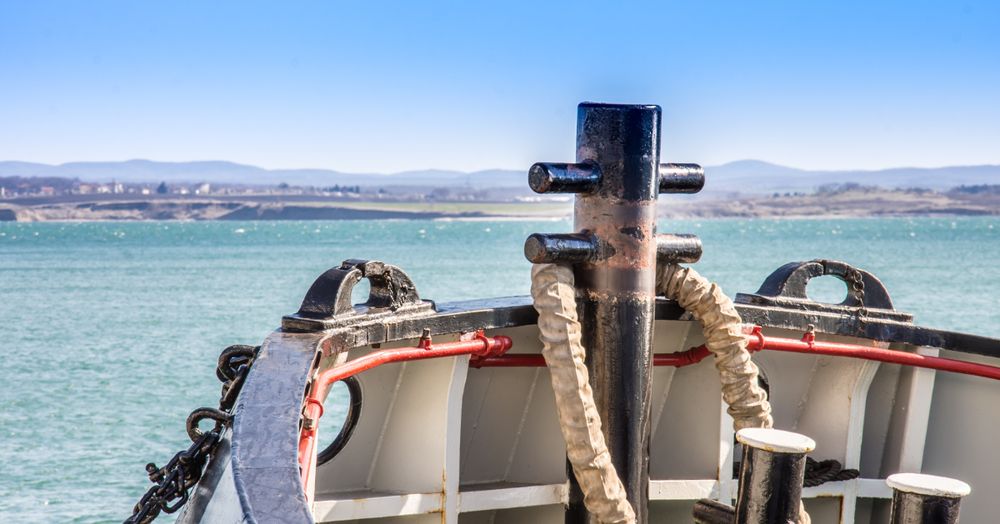
We’d love to answer any of your questions! Contact us now
P.S. Do you know of other people that will find this article useful? Please share it on social media. Thank you!