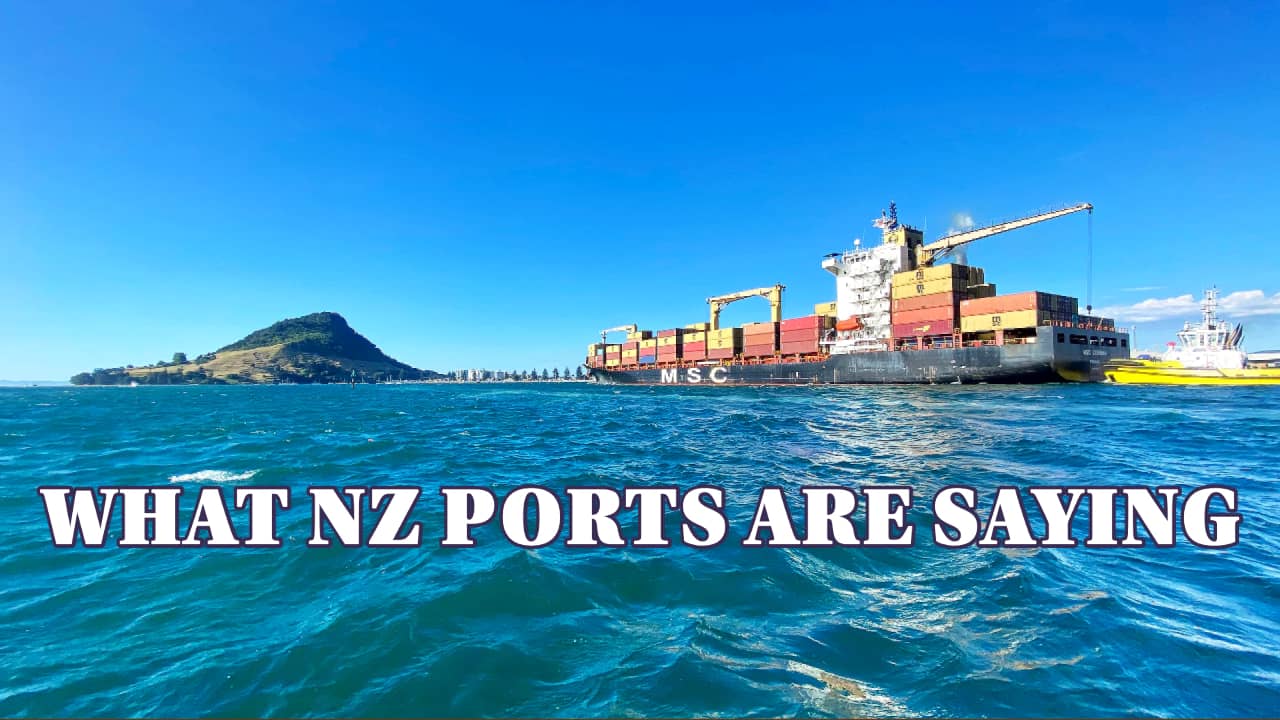
‘Whole of NZ’ Approach Needed to Fix the Supply Chain in NZ
5-minute read
The two years of the COVID -19 pandemic have created a ‘pressure cooker’ of unpredicted issues for ports, and this year’s annual conference of the Customs Brokers and Freight Forwarders organisation provided a sounding board.
Different in size and business profile, the country’s ports are all in the same frustrating pickle when it comes to the complexity of shifting cargo at the border.
Napier Port chief executive Todd Dawson, speaking on a panel of port leaders, promoted a ‘whole of NZ’ approach to the key issues.
“Less vessels, but bigger exchanges and upstream pressures – will it ever return to normal?”
He believes the quickest way to alleviate the pain in the supply chain is to get the nation’s ports back onto a ‘windows’ basis of operations, where vessels are booked into berthing slots for their arrival.
Napier Port has had some home runs this year, having opened a modern new 6 Wharf after getting it built on time and within budget – though only after years of working through the regulatory morass of the Resource Management Act.
The port services a fast-growing economic region and has built a very broad business across containerised trades, bulk cargo and (about to return) cruise liners.
6 Wharf was built, he said, to support economic growth and provide a healthy return to public-private shareholders. He says daily rail of cargo to Palmerston North is getting good support. There’s huge growth in the logging sector, and horticulture is expanding.
Yet New Zealand urgently needs additional infrastructure – which it is ‘decades behind’ in not being built.
Roger Gray, chief executive of Ports of Auckland, said the port system needs a 24/7 supply chain attitude across the country. “The ports are operational 24/7, as are the shipping lines, but the (NZ) supply chain is not.”
Speaking only a few days after the release of a damning report on the port’s failed partial automation project, Mr Gray fronted his comments by stating Ports of Auckland was now focused on a turnaround strategy for a port “that effectively lost its way and became inwardly focussed on automation”.
“The automation project just didn’t work, it was not known when it would, and it was causing distractions.
“We’re in the process of rebuilding, and we need to regain our mana.
“Our first pillar is having customers at the core. We need to be fit, and we’ve done some restructuring, reduced our head office numbers significantly, training our staff up and recruiting to ensure we’ve got enough straddle and crane drivers. We’re going back to basics. We very focused on the port.”
He said Auckland will progressively transfer operations over the next year or so, providing us another 10-12 years of capacity. “We won’t be clogging up, we’ve got plenty of capacity and plenty of infrastructure.”
He noted throughout returning, and in a recent week, the port had processed 9,500 TEU and is on track to reach 10,500 TEU/week by Christmas. POAL plans to return to berth windows in March.
Port of Tauranga general manager commercial Blair Hamill said that staff at the port’s container terminal have been “incredibly hard over the last couple of years to transact the same volume that was transacted the last four years.
“It may surprise some people that our volumes have been flat for the last four years. Yet the yard intensity is a lot higher than is optimal, so from the start of this CY22, we’ve been carrying ~17,000 TEU in the yard, and that’s over a 50% increase on what we saw pre-Covid days.
“Obviously, yard intensity impacts productivity, and our net crane rates April-August have been in the 20’s to 31 moves per hour and vessel rate of 55 to 65 across the same period.”
This is lower than what Tauranga has seen historically and clearly lower than they’d like it to be. Yard intensity is having an impact on productivity at the NZ port, considered for many years to be a leader in box exchanges.
Mr Hamill says NZ ports are acutely aware that labour is tight. “When we look at base-line 2018, across on-boarding straddles and cranes, we’ve seen a 12-17% increase in our labour resource, additional labour to transact the same volume.
“If we could return to the pro-forma windows we had over two years ago, we’d need less labour than we need today to transact the same sort of volume.”
Currently, 16 services access POT’s terminal; of these, six (37%) can consistently make their old pro-forma windows. “So, we have windows suspended as that’s not enough of a percentage to put all services back on window.”
Currently, Tauranga’s anchor wait time varies at an average of three days, with some zero days as vessels bunch on arrival off-schedule and impact wait time at anchor.
In the June financial year, pro-forma container vessel calls scheduled at 776 saw POT achieve 594, i.e. 172 fewer calls than were scheduled pro-forma.
Tauranga is looking to extend its terminal berth by 220-280 metres. The port has an Environment Court hearing date of February 27, 2023. Coupled with that, the port will embark on an automation project, looking to implement and install automated stacking cranes. A Request for Tender is being worked up.
On the assumption of clearing the regulatory threshold for this work, Tauranga’s capacity would double from 1.4 million TEU to 2.8 million TEU.
Mr Hamill said it was “absolutely essential for NZ exports and imports flows. Currently, we track 70% of NZ’s dairy trade (2.3 million tonnes), 61% of meat exports (550,000 tonnes), 30% of export logs and 55% of NZ kiwifruit exports. All up, $30 billion in value of key freight.”
Andrew Locke, GM Commercial at CentrePort, provided a macro overview of global freight issues. His insights included a perspective that 70% of all NZ shipping capacity is largely reliant on only seven shipping lines.
“The middle-sized lines have vanished.”
Another insight was that the shipping lines were pushing hard on carbonisation change. “A lot of ports think that if they obtain the cargo, they’ll get the ships (calling)”.
But, in the long term, it will the green energy capacity of a port, which will attract vessels. The formula would switch to: green energy charges = ships = cargo.
CentrePort is now up and running on its newly rebuilt infrastructure, and its container terminal was achieving 900 moves over a 24-hour period.
Simon Munt, general manager of Container Operations at Lyttelton Port Company, said LPC has achieved 12% volume growth over the past year with similar challenges of cargo flow and schedules. This was achieved on 80% of prior vessels, with larger exchanges and larger volumes.
This has put pressure on facilities, but “productivity has held up well through the last 2-3 years.
“We can blame Covid, and we can blame Auckland (congestion), but as a country, we’re behind in delivery of infrastructure, too slow to deliver infrastructure, and when we do, we’re doing it in brownfield environments.
“At LPC, we’re working really hard to stay ahead in terms of capacity and are continuing to invest. It’s a challenge for all to think about in regard to supply chain and how do we create some resilience?
“We’re all aware of the scheduling issues the shipping lines have had, and it’s a vicious circle. Until the ports can deliver productivity, shipping lines aren’t going to get on schedule.”
His insight is that a solution can only be addressed by a network.
“The last two years have shown that the port system is a network.”
For LPC’s part, the focus will be on the eastern expansion of its terminal to add an extra 15% of capacity, provide support for the return of windows and emphasis on its landside activities as a big depot operator.
“Unlike the challenges faced in Auckland and Tauranga, LPC is in a great spot in holding (development) consents for the next 30 years.” Ready for a bigger role in the national supply chain.
Source: The New Zealand Shipping Gazette
P.S. Easy Freight Ltd helps New Zealand importers & exporters to save money on international freight and reduce mistakes by guiding how to comply with Customs and biosecurity rules.
➔ Contact us now to learn how we can assist you.