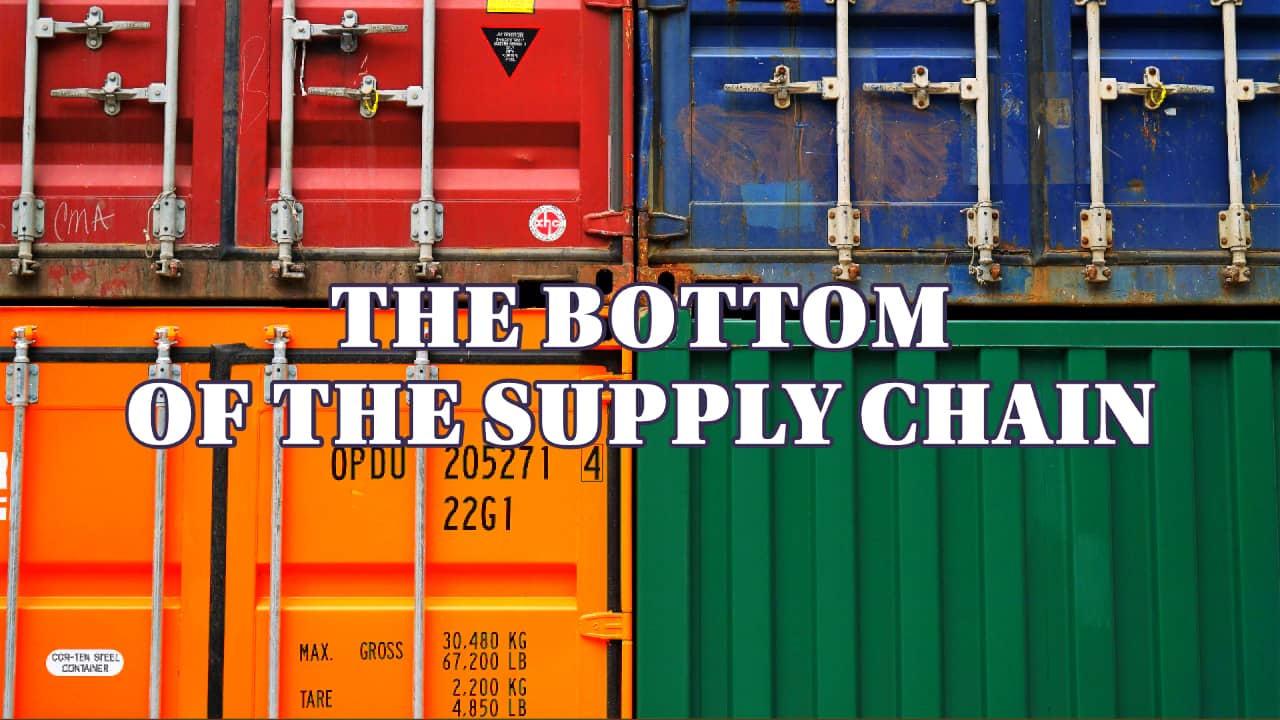
Does New Zealand Have an Empty Depot Problem?
7-minute read
The inability of the New Zealand ports sector to efficiently handle container throughput since the onset of the pandemic and carriers pressuring leanest rates from depots have contributed to serious congestion and capacity issues within the industry.
Such is the strident viewpoint of at least one senior executive in the depot sector, whom the Shipping GazetteTM agreed to quote on the basis of anonymity.
“With the disruption that the shipping community has experienced with COVID and the Ports of Auckland terminal etc., we have seen major congestion within the depot network, shipping lines with an inability to evacuate empty containers and, of course, that has placed a lot of pressure on the Port of Tauranga as well,” he said.
“If [carriers] have a vessel that is in the stream for eight to ten days, that means there are less sailings to New Zealand, so less slots to shift equipment out. Equipment then has to go somewhere, and so it lives in the container parks, and so we have a congestion issue.
“That goes right through the supply chain and means that containers are backed up with exporters trying to get loaded, and demurrage kicks off all over the place.
“We are still able to handle it in other parts of the country, but of course, if vessels are bogged down and tied up in the stream in Auckland and Tauranga, then there is a delay in a vessel, say arriving in Timaru or two vessels come on top of each other or whatever it may be.”
However, notwithstanding such issues, the executive emphasised that an underlying lack of depot capacity was a problem that dated back almost a decade – for which he apportioned considerable blame on the carriers.
“That’s got to be the shipping lines’ problem. They’ve kept rates horribly depressed and really denied entry-level by new participants because it is just not commercially viable. The shipping lines have said, ‘it is sort of working, and that’s okay, but it’s getting to the point now where it is exploding, and the shipping lines are saying, ‘you depots haven’t done enough work’.
“[But] you people created the climate where the infrastructure around you all has not kept pace with the growth required – we haven’t seen a new depot player for 20 years [with depot numbers in Auckland also declining from 11 to two since the mid-1990s].”
While noting carriers had now been “forced to become a little more commercially aware” and were consequently “willing to pay a little more”, the executive questioned how well the depot sector could respond in current circumstances.
“Auckland’s land costs and rental rates have skyrocketed, and the availability of land in the greater Auckland region has shrunk to crisis point for empty container storage – so those things are compounding into the perfect storm.
“Volumes are going to slow as we have a slightly slowing economy, and internal consumption might slow as the volumes come off slightly, but the underlying problem is still there.
“And we will get another peak of activity when the next boom comes along, and the problem is still going to be there, and it is going to manifest itself into a bigger hiccup for the industry.”
Empty depots are an important link in New Zealand’s supply chain that should not be overlooked as the Ministry of Transport works on a draft National Supply Chain Strategy, due to be presented to Transport Minister Michael Wood at the end of the year.
The dwindling supply of affordable land makes it difficult for empty container depots to establish themselves near ports. That threatens to pose a potential logjam in the supply chain, creating inefficiencies in the flow of empties back to areas of need for exporters.
Container depots play a vital role in New Zealand’s supply chain. They are the link through which the empty containers are off-hired by importers after being unpacked.
An efficient flow of boxes is important to ensure New Zealand exporters have the containers they need to load their outbound freight. Any impediment to that flow leads to significant problems elsewhere. Exports can’t move if exporters don’t have boxes to put them in.
Impediments do arise, and since COVID hit, those impediments have got worse.
Vessels which are delayed and off-window and facing days at anchor waiting for a berth both here and overseas can’t offload. When they can, they may do it at an alternative port (for example, skipping Auckland and discharging at Northport).
But they may also skip another port, or omit several ports on a planned voyage pattern, to get somewhat closer to their intended schedule. What happens to the flow of boxes then, when the positioning of empties can’t occur, and the export loads aren’t being picked up?
When it gets very bad, with empties stuck in Auckland, for example – Auckland being the country’s main import port, and therefore the natural centre for offhires to empty container depots – some lines have had to resort to “extra loaders”. These are vessels sent mainly to evacuate empties and reposition them elsewhere.
The repositioning may not even be to a New Zealand port. Boxes are required worldwide and, by their nature, are useable anywhere. So there is no guarantee that if a line sends a vessel to do a large-scale evacuation, the boxes will go to Kiwi pack points.
If another trade lane is more profitable and is short of equipment, the chances are that the boxes will be directed there to earn more revenue for the carrier. A senior shipping line executive confirmed that carriers do see NZ as a less profitable tradelane at present.
That gives a high-level lens over the current situation. However, a much longer-term issue relating to depots needs consideration in the National Supply Chain Strategy, according to the NZ Shipping Gazette.
The dilemma facing depots is that they are being priced out of land close to the ports and the industrial heartlands of our cities.
Are empty container depot operators able to pay the asking price for parcels of land that could house a factory, an office block or some other commercial proposition?
Land costs and rental rates in cities such as Auckland are prohibitive for a sector that has traditionally earned very low margins. One industry insider described depots as “the bottom of the food chain”, and the rates they have been able to command have hardly moved for years.
When depots have tried to improve their financial standing, it has usually been met with staunch resistance.
In 2009, for example, a couple of depot companies tried to take a leaf out of their Australian counterparts and apply an “infrastructure levy” for inward container lifts.
The Port of Brisbane had raised port rents by 390-400% as part of a value-raising process ahead of the sale of its 99-year lease. The Brisbane container depots saw this as a huge blow to their viability and planted an AU$25 surcharge on inbound containers to compensate.
Empty container depots in Sydney followed suit and the NZ depots tried to take a leaf out of their books.
They argued that tariffs had remained static for two decades. During that time, they had to absorb increased rents, higher local council compliance costs and rates, environmental costs such as the requirement to seal ground surfaces, wage and ACC rises, and investment in IT to introduce paperless processing systems.
The response of the container lines was very clear – they didn’t like it, didn’t think it was justified, felt it broke contracts and suggested that collusion was at play because of the timing.
The International Container Lines Committee (ICLC) in NZ commented:
“Such cost increases do nothing for the competitiveness of New Zealand’s supply chain unless, of course, there is a clear improvement to the value proposition of the depots, which in this case does not appear to be the case . . .”
The depots grumbled in response something like,
“If the lines had been halfway reasonable and prepared to negotiate rate increases at regular intervals to cover increased costs instead of the requirement continually falling on deaf ears, the present dilemma could have been avoided”.
Instead of rate increases, the now-prevalent VBS (vehicle booking systems) have perhaps been a financial saviour for the depots. They have provided a flow of income, albeit adding that cost to the truckers who have then had to seek reimbursement from their customers.
Another change has been that the depot sector has consolidated as smaller operators have closed shop, exited the industry or been bought out, to the extent that there are just two major players in addition to the operations run by port companies.
Each has made efforts to improve its efficiency, introduce new software and open new facilities where possible.
They also endeavour to make the most of their existing footprints, using space to its maximum.
But the fact is that container volumes will increase over time as New Zealand’s trade grows, so there is a requirement to plan for more container depot capacity in locations convenient for access to and from our major ports.
Major new inland facilities such as Ruakura will have a vital role to play, for sure. But what about land adjacent to city industrial areas such as Southdown and Penrose or close to Sulphur Point?
Suppose depot companies cannot afford to stay in those areas. In that case, they will be driven further out, into peripheral areas of the cities, which will mean cheaper land or rental costs but will increase transportation costs and time for offhires and pick-ups.
What is the solution if we accept that the current capacity will be insufficient for the needs of NZ supply chain efficiency?
If depots are indeed “the bottom of the food chain”, it is important they aren’t forgotten. They remain an important link in the NZ supply chain – and a chain is only as strong as its weakest link.
Source: The New Zealand Shipping Gazette
P.S. Easy Freight Ltd helps New Zealand importers & exporters to save money on international freight and reduce mistakes by guiding how to comply with Customs and biosecurity rules.
➔ Contact us now to learn how we can assist you.