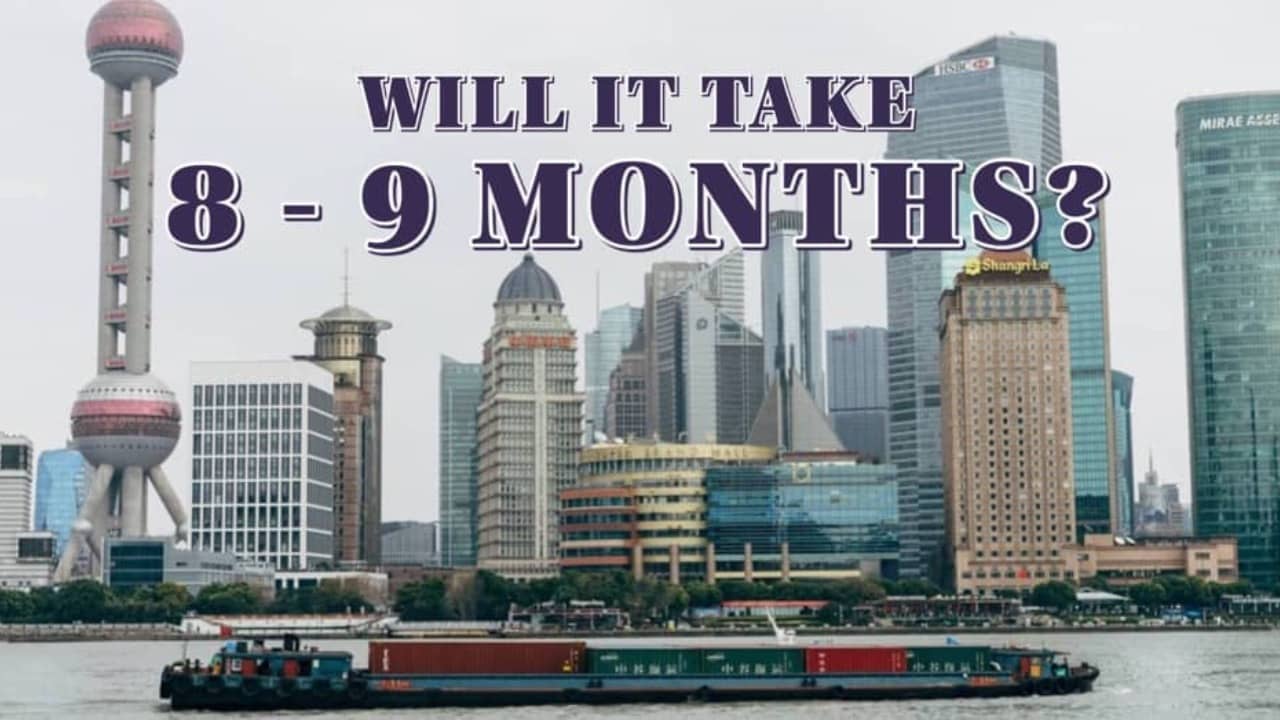
Longer Phase on Restoring Schedules
4-minute read
Returning disruptive elements in the supply chain to anything resembling normality will take a lot longer than shippers, freight forwarders, ports, and governments will hope. One of the key disruptors, schedule reliability, is in the spotlight.
Even though supply chain problems continue to plague the industry, it appears that COVID is now entering an endemic phase rather than a pandemic, says Alan Murphy, CEO, Sea-Intelligence.
As such, it is also the time to take stock and contemplate how long it will take the supply chain to normalise, he says.
“The system is so far out of balance that there is no historical precedence fully describing this situation, however one element can be used to create a realistic baseline, and that is the U.S. West Coast labour dispute of early 2015, which led to major delays and bottlenecks.”
The peak impact of the labour dispute was felt in February 2015, with reliability 70 percentage points below the baseline.
Following the dispute resolution on February 20, it took 8-9 months for reliability to get back to the baseline.
“Currently, schedule reliability on Asia-North America West Coast is just 10.1%, which is not different from the 12.6% recorded in February 2015, suggesting a return to pre-pandemic normality would also be 8-9 months.
“That said, the market is showing no indication that we have started on the path to resolution.”
And with the Omicron variant flaring up across China, major manufacturers are shutting factories, ports are clogging up, and workers are in short supply as officials impose city lockdowns and mass testing on a scale unseen in nearly two years.
The prospect of continued disruptions in the world’s second-largest economy, which has a zero-tolerance strategy for combating the pandemic, heightens fears that the disruptions will ripple through the global economy.
Companies, including memory-chip maker Samsung Electronics Co., German automaker Volkswagen AG, and a textiles company that supplies Nike Inc. and Adidas AG, are suffering production hitches.
Since late December, officials have taken measures to counter Covid-19 outbreaks in several Chinese cities, including the eastern port of Tianjin, Xi’an in central China, and the southern technology hub of Shenzhen.
The world’s third-busiest container port of Ningbo-Zhoushan, near Shanghai, risks worsening backlogs from truck restrictions and warehouse operations after more than two dozen Covid-19 cases were confirmed in the surrounding area.
Chinese authorities are adhering to the same playbook that successfully curtailed initial outbreaks of the pandemic and caused intermittent disruptions to production and supply chains.
The potential consequences are more severe this time, economists warn, because of the highly contagious nature of Omicron, which has been detected in some areas of China. The variant is hitting the country as Beijing seeks to contain outbreaks during the Winter Olympics.
Several economists said China might escalate its containment policy, and some have touted the possibility of a nationwide lockdown, unseen since April 2020.
Toyota Motor Corp. said operations on Monday and Tuesday at its joint-venture factory in Tianjin came to a halt because of mass testing requirements imposed across the city.
About 14 million residents in Tianjin, an industrial hub in northeastern China that accounts for 1.7% of China’s exports, were tested after two cases of the Omicron variant were detected.
A Volkswagen plant based in the city was also closed, Stephan Wöllenstein, the auto maker’s China chief executive, said on Tuesday. He said that the German carmaker recently also closed a plant in Ningbo, a port city in eastern China, after another small Covid-19 outbreak.
This week, more than five million people living in China’s central city of Anyang entered a citywide lockdown after more than 80 cases were confirmed locally, including two Omicron cases.
In Henan’s capital city Zhengzhou, where many of the world’s iPhones are assembled by Foxconn, the local government required all city residents to undergo Covid-19 tests.
Mr Wöllenstein added that in many cases, Chinese authorities had brought local outbreaks under control in a few weeks, allowing businesses to restart operations.
As western consumers and retailers have become more dependent on China since the start of the pandemic, business executives and industry analysts expect further disruptions could rattle China’s manufacturers and ports as new outbreaks emerge.
The economic risks of sticking with strict Covid-19-related restrictions within China are also growing.
“We are monitoring very carefully what’s happening over there because Omicron has the potential to significantly change the picture in China compared to 2020 and 2021,” said Guillaume Faury, CEO of Airbus SE, the world’s largest plane manufacturer.
“The risk posed by the Omicron variant is that we could take a huge step back in terms of supply-chain bottlenecks,” said Frederic Neumann, co-head of Asian Economics Research at HSBC.
“This time, the situation could be even more challenging than last year given China’s increasingly significant role in global supply.”
Source: The New Zealand Shipping Gazette and The Wall Street Journal
P.S. Easy Freight Ltd helps New Zealand importers & exporters to save money on international freight and reduce mistakes by guiding how to comply with Customs and biosecurity rules.
➔ Contact us now to learn how we can assist you.