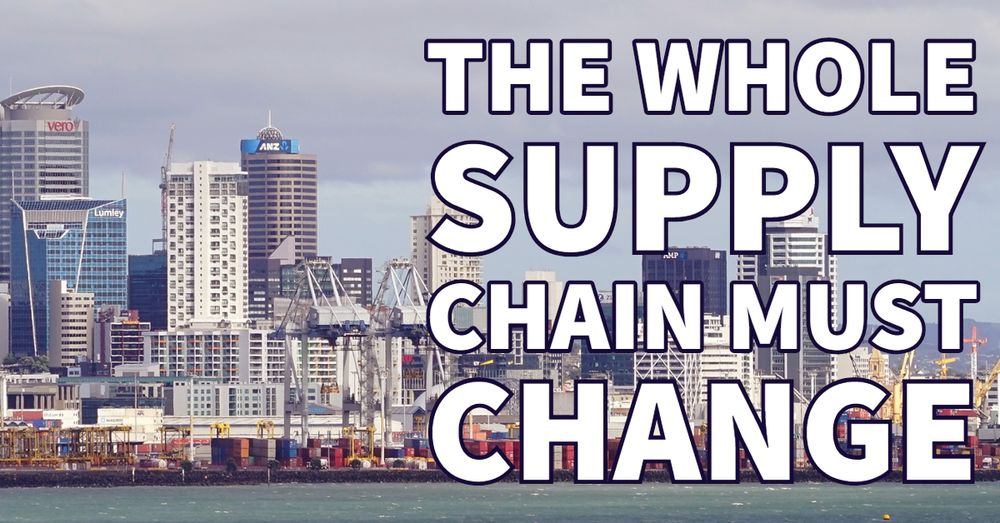
Reasons for the Import & Export Freight Hold Ups in Auckland
6-minute read
The fragility of New Zealand’s supply chain has been exposed several times in recent years, for example through the Canterbury and Kaikoura earthquakes which hammered the ports of Lyttelton and CentrePort, and the 2012 Auckland industrial troubles which disrupted operations there and put huge pressure on the Port of Tauranga as a back up.
That fragility has been highlighted again by the recent situation at the Ports of Auckland where a “perfect storm” of issues hit an unfortunate nadir with the tragedy of the straddle driver fatality. The accident and the understandable impact on staff at the port saw operations temporarily grind to a halt.
Quickly, the ramifications spread to the Port of Tauranga which had to handle the import calls of vessels that could not obtain a berth in Auckland. Tauranga began to suffer from congestion as a result.
The situation became heated among shippers and importers and my mailbag received one irate email from a person concerned that there were inadequate information flows on the congestion in Auckland and arguing that much better engagement was needed so that other parts of the supply chain could prepare contingencies to handle diverted cargoes.
Given that the situation in Auckland is going to be difficult for quite some time, that’s a valid point. I’m aware that the Ports of Auckland and National Road Carriers, representing the trucking industry, have recently been talking to explore how there can be more co-operation and transparency in future.
The bottom line is that the market as a whole may have to understand the issues in Auckland better, and may have do some things differently in order for the supply chain to function better in future.
So let’s try to achieve that greater understanding by analysing the factors in this perfect storm, and why the port is operating at capacity.
First of all there is the yard automation project underway at Ports of Auckland. Areas of the port have had to be reserved for construction and trialling of the new automated straddles.
A straddle guidance system — a ground-based GPS — is being installed, requiring trenching for 25km of fibre optic cable and new lighting towers with radio transmitters.
The net effect is that somewhere upwards of 20% of the yard space is compromised and to compensate the port has to stack boxes higher. This impacts productivity because the higher the stack, the more moves are required when boxes in the middle of the stack need to be retrieved.
Also, traditional straddles have to divert around the civil works, meaning that box moves are slower. Add to that the prevalence of ships arriving at the port off-window — i.e. outside the time for which a berth has been reserved. In the last 12 months over half of ships arrived outside their planned arrival time.
This is not usually the fault of the shipping lines. They usually set up their schedules to a fixed-day weekly rotation and book berth windows accordingly. However, typhoons in North Asia or berth delays overseas make ships run late.
Late ships make it difficult for ports to provide the right amount of labour to service ships and trucks. The berth windows are calculated based on expected cargo exchanges for which the required labour force can be organised in advance but late arrivals mean pulling in people at short notice.
Late ships clash with the arrival of other on-time vessels which leads to ships having to wait (or divert), berth congestion, further yard congestion and delayed exchanges via road and rail.
All of this is occurring against a general trend of rising container volumes which all ports have to deal with.
For those reasons, Ports of Auckland was already hitting capacity before the straddle tragedy. When operations ground to a halt because of that, the fragility of our supply chain was fully exposed, and the Port of Tauranga suddenly faced the added pressure too.
Let’s turn the spotlight on another part of the supply chain, namely the trucking industry because it too is grappling with many difficult issues.
It is facing cost increases across the board – fuel price rises (exacerbated in Auckland because of the regional fuel tax), road user charges increases and a shortage of drivers.
There is chronic congestion on Auckland roads which holds up trucks, creates delays in picking up and dropping off boxes and reduces productivity. Costs of doing business in Auckland are rising. Truckers can’t easily deal with added pressures.
However, due to the automation project the truck grid has lost some slots. This has been an area of some controversy in the past as truckers and the port have tried to find a compromise solution between the ideal of getting a slot at short notice and the port’s need for forward bookings and maximum use of slots.
Earlier in the year there was much publicity given in changes made to the VBS (vehicle booking system) whereby the port was trying to improve the efficiency of truck exchanges and avoid “bulk bookings” which sometimes led to slots being unused.
Each slot is now required to be allocated to a specific container number for both imports and exports. Truckers and their customers have had to adjust to VBS slots being released 48 hours prior to the booking day and issued on a first-in first-served basis.
That in turn has meant changes required from shippers and importers. They have to pass on information 48 hours prior such as dates for dropping off empties and pick-ups of fulls. MPI and shipping line “holds” must be released in order for truckers to book a slot.
These are examples of the supply chain having to change under pressure, and indeed doing so, from the port to the trucker to the shipping lines and to the shipper.
Perhaps that gives us something of an indicator for the future — the ability of the supply chain to adapt.
The truth is that there has to be adaptation because the reality is that the supply chain, particularly in Auckland, is going to face difficulties for some time ahead.
POAL’s automation project means that its infrastructure will be compromised until the project is complete towards the end of 2019. It can’t be accelerated.
Other supply chain pressures may come from left field — for example stink bug season is with us again, particularly for car carriers. Earlier this year there were delays with contamination treatments and ships were refused entry, leading to a subsequent bunching of arrivals and a sudden cut of supply to the imported car industry.
It is easy to see how a one-off incident can quickly snowball and become a major problem for the rest of the supply chain.
What can help the situation is better transparency and an information flow so that all parts of the supply chain, from ports through to truckers and on to the shippers and importers, understand the extent of the situation and can put in contingencies, where possible, to work earlier on the arrangements for bookings and transfers.
I spoke to Ports of Auckland about this and it accepts there are lessons to be learned from the recent situation. National Road Carriers, as mentioned before, has joined with the port to try and see where there can be co-operation to find solutions.
The guts of it is that the supply chain in Auckland particularly is fragile. There is light at the end of the tunnel for the port thanks to automation, but automation only fixes the port.
There is a need for much better co-ordination between all parts of the supply chain while the work is done.
Auckland roads will still be congested and there will still be a shortage of truck drivers.
If Auckland is to keep moving over the next 30 years, with the arrival of another million citizens, the supply chain is going to have to step up to a whole new level of planning, organisation and cooperation.
The changes forced by Ports of Auckland’s automation project are just the beginning.
Source: NZ Shipping Gazette
P.S. We’d love to answer any of your questions! Contact us now. Do you know of other people that will find this article useful? Please share it on social media. Thank you!